Model Konseptual Analisis Perbaikan Kinerja Industri Gula
1. PENDAHULUAN
Industri gula Indonesia merupakan industri manufaktur yang berkembang pertama kali di Indonesia. Ditinjau dari aktivitas ekonomi, industri gula ialah industri yang memberikan imbas ganda cukup signifikan secara nasional kepada penciptaan output, pemasukan, nilai tambah dan tenaga kerja mengenang gula merupakan suatu komoditi pangan yang penggunaannya sungguh luas. Berdasarkan analisis keterkaitan antara industri melalui analisis input-output menunjukkan bahwa secara nasional industri gula mempunyai keterkaitan eksklusif dengan sektor-sektor dibelakangnya sebanyak 53 sektor (dari 172 sektor) dan keterkaitan langsung ke depan dengan 30 sektor.
Hal ini menawarkan bahwa gula selain untuk menyanggupi kebutuhan konsumsi selesai, juga dibutuhkan untuk mendorong kenaikan produksi industri-industri yang menggunakan gula sebagai materi bakunya. Pada kala kejayaannya (tahun 1930- an) Indonesia pernah menjadi negara eksportir gula ke dua di dunia setelah Kuba. Namun, semenjak tahun 1967 Indonesia menjadi negara pengimpor gula untuk memenuhi kebutuhannya. Ketergantungan ketersediaan pangan terhadap impor ialah salah satu indikator yang digunakan untuk mengukur ketahanan pangan.
Dengan usulanutama untuk memperkuat ketahanan pangan, Indonesia berusaha mengembangkan bikinan gula dalam negeri, termasuk mencanangkan target swasembada gula, yang sampai kini belum tercapai. Permasalahan yang dihadapi industri gula nasional ditandai dengan ketidakmampuannya untuk menyanggupi kebutuhan gula yang disantap masyarakat maupun materi baku industri. Kondisi lima tahun terakhir menunjukkan bahwa rerata ketergantungan Indonesia kepada impor gula untuk menyanggupi kebutuhannya mendekati 50%.
Kajian lebih lanjut tentang urusan yang dihadapi memberikan rendahnya produktivitas dan efisiensi pabrik gula (Stakeholder’s Pergulaan Nasional 2006; P3GI 2008; Effendi 2009) sebagai penyebabnya. Sink dan Thomas (1989) menyebutkan bahwa produktivitas dan efisiensi ialah dua aspek penting dalam kinerja. Rendahnya produktivitas dan efisiensi pabrik gula saat ini dibandingkan pencapaian di tahun 1930-an memperlihatkan bahwa produktivitas dan efisiensi pabrik gula berada di bawah peluangyang bisa diraih. Oleh alasannya adalah itu, perbaikan kinerja industri gula merupakan hal yang memiliki peluang dilakukan.
Perbaikan kinerja dapat dijalankan dengan banyak sekali cara, namun kebanyakan terdapat lima tahap (Swanson 1996) yaitu
- Tahap analisis,
- Tahap rancangan,
- Tahap pengembangan,
- Tahap implementasi, dan
- Tahap evaluasi.
Selanjutnya, Swanson (1996) menyebutkan bahwa tahap analisis merupakan tahap paling penting. Tujuan dari tahap analisis adalah untuk menentukan kinerja, target kinerja, dan prioritas perbaikan kinerja. Beberapa observasi yang telah dilaksanakan pada pabrik gula di Indonesia memberikan bahwa penelitian yang bekerjasama dengan analisis perbaikan kinerja (selaku proses yang dipakai secara sistematis untuk mengidentifikasi kinerja, memilih sasaran kinerja yang diharapkan, dan untuk memilih prioritas perbaikan) belum pernah dikerjakan. Penelitian ini bertujuan untuk menghasilkan versi konseptual yang dapat dipakai untuk melaksanakan analisis perbaikan kinerja industri gula. Model yang dihasilkan merupakan model yang terintegrasi untuk mencapai tujuan dari tahap analisis perbaikan kinerja.
2. TINJAUAN PUSTAKA
2.1 Penentuan Kinerja
Untuk menentukan kinerja perlu dilakukan pengukuran kinerja. Pengukuran kinerja merupakan sub sistem dari manajemen kinerja (Cokins 2004; Halachmi 2005; Stiffler 2006; Baxter dan MacLeod 2008). Pengukuran kinerja didefinisikan sebagai proses untuk mengkuantifikasi efisiensi dan efektivitas dari suatu tindakan (Tangen 2004; Olsen et al. 2007; Cocca dan Alberti 2010). Dikaitkan dengan administrasi operasional, Radnor dan Barnes (2007) mendefinisikan pengukuran kinerja sebagai proses mengkuantifikasi input, output, dan tingkat aktivitas dari sebuah proses.
Wibisono (1999) menyebutkan bahwa pengukuran kinerja di perusahaan manufaktur pada level manajemen operasi dapat dibagi menjadi tiga jenis yakni:
- Pengukuran kinerja taktis (competitive priorities),
- Pengukuran kinerja operasional (manufacturing task), dan
- Pengukuran kinerja strategis (resource availability).
Hal yang sama juga dikemukakan oleh Craig dan Grant (2002) bahwa keunggulan berkompetisi sebuah organisasi disokong oleh kemampuan sumber daya dan kegiatan berkala organisasi. Terdapat tiga faktor formal dari pengukuran kinerja (Spitzer 2007) adalah
- Ukuran-ukuran (variabel yang diukur),
- Proses pengukuran (tahapan yang menawarkan bagaimana cara melakukan pengukuran), dan
- Infrastruktur teknis (berupa hardware dan software komputer yang dipakai untuk mendukung proses pengukuran).
Tiga persyaratan yang dapat digunakan untuk menganggap keefektifan dari tata cara pengukuran kinerja (Olsen et al. 2007) ialah:
- Keterkaitan,
- Perbaikan terus-menerus, dan
- Pengawasan proses.
Terkait dengan ukuran-ukuran (variabel) yang diukur, Medori dan Steeple (2000) menyatakan bahwa pada semua framework pengukuran kinerja yang sudah dihasikan, pada umumnya memiliki kekurangan dalam hal menunjukkan bimbingan kepada pemilihan variabel kinerja yang akan diukur. Denton (2005) menyatakan bahwa meskipun banyak hal yang dapat diukur tetapi lebih penting untuk mengukur hal yang spesifik dan relevan.
Berdasarkan pengalaman implementasi pada beberapa perusahaan di Indonesia ditinjau dari aspek kemudahan dan nilai tambah yang diberikan, Wibisono (2006) menyatakan bahwa pendekatan yang sesuai untuk dipraktekkan di Indonesia dalam menentukan variabel kinerja yang mau diukur yakni dengan melaksanakan identifikasi variabel kinerja dari tiga perspektif yakni
- Keluaran organisasi (business results),
- Proses internal (internal business processes), dan
- Kemampuan atau ketersediaan sumber daya (resources availability).
Radnor dan Barnes (2007) menyebutkan bahwa terdapat tiga kecenderungan biasa dalam pengukuran kinerja yaitu
- Keluasan dari unit analisis (level individu, stasiun kerja, lini produksi, unit bisnis, perusahaan),
- Kedalaman ukuran kinerja (keterkaitan variabel kinerja),
- Peningkatan range ukuran kinerja (contohnya dari efisiensi menjadi efisiensi dan efektivitas).
Dalam hal range ukuran kinerja, beberapa observasi terdahulu memperlihatkan adanya kekurangan dalam versi pengukuran kinerja pabrik gula alasannya cuma dilaksanakan dengan memakai range ukuran kinerja yang sempit yakni
- Produktivitas (Yusnitati (1994) dan Manalu (2009) terkait dengan kinerja output per input,
- Efisiensi buatan (Siagian, 1999) terkait dengan kinerja proses, dan
- Efisiensi teknis (LPPM IPB, 2002) terkait dengan kinerja proses.
Berdasarkan kedalaman ukuran kinerja, pada observasi terdahulu tidak memperhatikan keterkaitan ukuran kinerja. Hal ini dapat menyebabkan upaya perbaikan yang dilaksanakan tidak menghasilkan perbaikan kinerja yang signifikan. Selain itu, jikalau merujuk pada pernyataan Olsen et al. (2007) mampu menjadikan berkurangnya keefektifan sistem pengukuran kinerja. Kerangka kerja proses pengukuran kinerja perlu diperbaiki secara kontinu dengan memikirkan berbagai model pengukuran kinerja yang sesuai dengan masalah yang dihadapi (Nenadal 2008). Beheshti dan Lollar (2008) menyebutkan bahwa pengukuran kinerja ialah keputusan penting yang sering memakai informasi subyektif.
Perbedaan satuan pada setiap ukuran kinerja yang dipakai menyebabkan proses aggregasi ukuran kinerja menjadi rumit. Oleh sebab itu versi keputusan yang memanfaatkan nalar fuzzy dapat memberikan penyelesaian yang logis. Chan et al. (2002) menganjurkan penggunaan logika fuzzy dalam penilaian kinerja dan Unahabhokha et al. (2007) memakai pendekatan fuzzy expert system untuk memprediksi nilai kinerja. Terkait dengan infrastruktur yang digunakan dalam pengukuran kinerja, Santos et al. (2007) menawarkan adanya variasi infrastruktur ialah secara manual dan pemanfaatan metode informasi.
Marchand dan Raymond (2008) menawarkan perubahan dalam pemanfaatan metode isu untuk pengukuran kinerja, adalah dari sistem berita administrator (1980-1999) ke Sistem Intelijen ( 2000-ketika ini). Selain itu, Denton (2010) menyebutkan bahwa intranet dan internet dapat digunakan untuk memajukan pengelolaan dan pengukuran kinerja.
2.2 Penentuan Target Kinerja
Sistem pengukuran kinerja ialah kunci untuk memandu dan menguji hasil dari proses perbaikan, tetapi tidak mengindikasikan bagaimana sebuah proses harus diperbaiki. Salah satu pendekatan yang mampu membantu melengkapi hal tersebut yaitu benchmarking. Dattakumar (2003) menyimpulkan bahwa pendekatan benchmarking dapat dipakai untuk perbaikan terus menerus. Hasil review Grunberg (2003) kepada metoda-metoda yang dipakai untuk perbaikan kinerja aktivitas operasional pada perusahaan manufaktur memperlihatkan bahwa pendekatan benchmarking juga memungkinkan untuk digunakan.
Aplikasi benchmarking dalam perbaikan kinerja telah banyak dilaksanakan. Dimulai pada selesai 1970 oleh Xerox Corporation yang menetapkan untuk membandingkan operasional perusahaan dengan L.L. Bean yang memiliki produk yang berlainan tetapi mempunyai karakteristik fisik yang serupa (Tucker et al. 1987 dalam Elmuti dan Yunus 1997). Oleh alasannya itu, pengelompokan organisasi yang mempunyai karakteristik yang serupa perlu dikerjakan sebelum proses benchmarking. Pengelompokan organisasi yang memiliki karakteristik yang sama mampu dilaksanakan dengan memakai tata cara clustering. Xu & Wunsch (2009) menyatakan bahwa pengelompokan (clustering) obyek kedalam beberapa kelompok (cluster) yang memiliki sifat yang homogen atau dengan kombinasi sekecil mungkin diharapkan untuk membuat lebih mudah analisis data.
Terdapat dua tahapan yang harus dikerjakan dalam analisis cluster yakni
- Memutuskan apakah jumlah cluster ditentukan atau tidak dan
- Menentukan algoritma yang akan digunakan dalam clustering.
Untuk memutuskan berapa jumlah cluster yang hendak dibentuk, Sadaaki et al. (2008) menyebutkan bahwa terdapat dua pendekatan yang mampu digunakan ialah supervised (jikalau jumlah cluster ditentukan) dan unsupervised (bila jumlah cluster tidak ditentukan/alami). Gan et al. (2007) menyatakan bahwa dalam melaksanakan analisis clustering mampu memilih satu diantara 2 pendekatan ialah
- Hard Clustering atau
- Soft Clustering (diketahui juga sebagai fuzzy clustering).
Pemilihan pendekatan yang dipakai tergantung jenis data yang akan dikelompokkan. Hard Clustering digunakan bila data berupa Crips sedangkan soft clustering dipakai bila data berbentuk fuzzy. Metode yang mampu digunakan pada pendekatan Hard Clustering (Gan et al. 2007) ialah
- Non-Hierarchical clustering (Partisional Clustering) dan
- Hierarchical Clustering.
Pada tata cara NonHierarchical clustering, terdapat 3 cara untuk menggolongkan data dalam satu cluster ialah
- Sequential threshold,
- Parallel threshold, dan
- Optimization.
Sedangkan dalam tata cara Hierarchical Clustering, Xu dan Wunsch (2009) menyatakan bahwa terdapat dua tipe dasar adalah
- Penyebaran (divisive), dan
- Pemusatan (agglomerative).
Tipe divisive mengawali pengelompokkan dari cluster yang besar (berisikan semua data) lalu data yang paling tinggi ketidaksesuaiannya dipisahkan dan seterusnya. Sedangkan tipe agglomerative mengawali pengelompokkan dengan menganggap setiap data sebagai cluster lalu dua cluster yang memiliki kesesuaian digabungkan menjadi satu cluster dan seterusnya.
Terdapat lima cara untuk menggabungkan antar cluster ialah
- Single linkage (berdasarkan jarak terkecil),
- Complete linkage (berdasarkan jarak terjauh),
- Centroid method (berdasarkan jarak centroid),
- Average linkage (menurut berdasarkan rata-rata jarak), dan
- Ward’s method (menurut total sum of square dua cluster).
Pemilihan pendekatan diputuskan berdasarkan kesesuaian dengan problem yang dihadapi. Hasil yang dicapai lewat penerapan praktek terbaik dari L.L. Bean adalah kenaikan efisiensi dan produktivitas (Tucker et al. 1987 dalam Yasin 2002).
Selain itu, menurut Dragolea dan Cotirlea (2009) faedah benchmarking antara lain yakni
- Perbaikan terus menerus untuk meraih kinerja yang lebih baik menjadi budaya organisasi,
- Meningkatkan wawasan terhadap kinerja produk dan jasa, dan
- Membantu dalam memfokuskan sumberdaya untuk meraih sasaran.
Pierre dan Delisle (2006) merekomendasikan tata cara diagnosa berbasis wawasan pakar untuk melakukan benchmarking kinerja. Organisasi atau perusahaan yang berlawanan memiliki metoda benchmarking sendiri, namun apapun tata cara yang digunakan, langkah-langkah utamanya yakni sebagai berikut :
- Pengukuran kinerja dari varibel-variabel kinerja terbaik pada kelompoknya relatif terhadap kinerja kritikal;
- Penentuan bagaimana tingkat-tingkat kinerja diraih; dan
- Penggunaan gosip untuk pengembangan dan implementasi dari planning peningkatan (Omachonu dan Ross 1994 dalam Elmuti dan Yunus 1997).
Hal tersebut sejalan dengan tujuan dari analisis perbaikan kinerja. Sebelum melakukan identifikasi bagaimana tingkat kinerja diraih (praktek terbaik), perlu dijalankan penyeleksian kinerja terbaik dalam kelompoknya. Proses penyeleksian alternatif terbaik dari beberapa alternatif secara sistematis untuk ditindaklanjuti sebagai sebuah cara pemecahan problem dikenal selaku pengambilan keputusan. Berdasarkan jumlah persyaratan yang digunakan, maka masalah keputusan mampu dibedakan menjadi dua klasifikasi, adalah dilema keputusan dengan persyaratan tunggal dan kriteria beragam (multikriteria).
Pengambilan Keputusan Multikriteria (MCDM) didefinisikan Kusumadewi et al. (2006) selaku suatu sistem pengambilan keputusan untuk memutuskan alternatif terbaik dari sejumlah alternatif berdasarkan beberapa kriteria tertentu. Yoon (1981) dalam Kusumadewi et.al.(2006) menyatakan bahwa masalah MCDM tidak selalu memperlihatkan sebuah solusi unik, perbedaan tipe bisa jadi akan menunjukkan perbedaan penyelesaian.
Adapun jenis-jenis penyelesaian pada dilema MCDM (Kusumadewi et al. 2006) yakni :
- Solusi ideal,
- Solusi non-dominated (solusi Pareto-optimal),
- Solusi yang lebih digemari , dan
- Solusi yang memuaskan.
Pada solusi ideal, kriteria atau atribut dapat dibagi menjadi dua kategori, yakni standar yang nilainya akan dimaksimumkan (kategori standar laba), dan patokan yang nilainya akan diminimumkan (kategori kriteria biaya). Solusi ideal akan memaksimumkan semua standar laba dan meminimumkan semua tolok ukur ongkos (Daellenbach dan McNickle 2005). Solusi feasible MCDM dikatakan non-dominated kalau tidak ada penyelesaian feasible lainnya yang mau menghasilkan perbaikan kepada suatu atribut tanpa mengakibatkan degenerasi pada atribut yang lain.
Solusi yang membuat puas yakni himpunan bab dari penyelesaian-penyelesaian feasible dimana setiap alternatif melampaui semua persyaratan yang diharapkan. Zimmermann (1991) dalam Kusumadewi et al. (2006) menyatakan bahwa menurut maksudnya, MCDM dapat dibedakan menjadi dua yakni : Multi Attribute Decision Making (MADM) dan Multi Objective Decision Making (MODM). MADM digunakan untuk menyelesaikan problem-duduk perkara dalam ruang diskret, sedangkan MODM dipakai untuk menuntaskan masalahmasalah pada ruang kontinyu. Secara biasa dapat dibilang bahwa MADM memilih alternatif terbaik dari sejumlah alternatif, sedangkan MODM mendesain alternatif terbaik.
Terdapat beberapa sistem yang dapat digunakan untuk menyelesaikan masalah MADM, antara lain yaitu :
- Simple Additive Weighting Method (SAW),
- Weighted Product (WP),
- ELimination Et Coix Traduisant la realitE (ELECTRE),
- Technique for Order Preference by Similarity to Ideal Solution (TOPSIS), dan
- Analytic Hierarchy Process (AHP).
Untuk melakukan pemilihan terhadap organisasi yang berkinerja terbaik (menjadi best in class), Laise (2004) beropini bahwa pendekatan tradisional yang digunakan untuk memilih organisasi yang menjadi best in class ialah pendekatan ranking memiliki kelemahan. Pada pendekatan tradisional (Laise, 2004), persoalan benchmarking dengan banyak standar diselesaikan dengan mengkonstruksi suatu indikator dengan merata-ratakan semua score yang diperoleh sebuah organisasi atas ukuran-ukuran yang berbeda.
Rata-rata ialah suatu ukuran kecenderungan terpusat dari sebuah golongan data dan cukup mewakili jikalau data memiliki suatu variabilitas yang rendah, namun bila dijalankan pengamatan dengan variabilitas tinggi, rata-rata bukan ukuran yang bagus. Menggunakan rata-rata mampu menghilangkan gosip yang pantas diperhitungkan dan oleh sebab itu tidak sesuai dipakai untuk menciptakan perbandingan. Selanjutnya, Laise (2004) menganjurkan penggunaan metode yang ialah pengembangan dari rancangan outranking adalah ELECTRE. Metode ELECTRE ialah golongan dari algoritma yang dikembangkan dalam Operational Research (Roy 1985; Vincke 1992; Roy dan Bouyssou 1993; Pamerol dan Barba-Romero 2000).
ELECTRE berdasarkan Kusumadewi et.al.(2006) didasarkan pada rancangan perankingan lewat perbandingan berpasangan antar alternatif pada persyaratan yang tepat. Suatu alternatif dibilang mendominasi alternatif yang yang lain kalau satu atau lebih kriterianya melebihi (ketimbang tolok ukur dari alternatif lainnya) dan sama dengan kriteria lain yang tersisa. Jafari et al. (2007) mengusulkan kerangka kerja untuk menentukan tata cara evaluasi kinerja terbaik menggunakan SAW. Konsep dasar tata cara SAW adalah mencari penjumlahan terbobot dari rating kinerja pada setiap alternatif pada semua atribut (Kusumadewi et.al., 2006).
Kelemahan pada tata cara SAW ialah membutuhkan proses normalisasi matriks keputusan ke sebuah skala yang mampu diperbandingkan dengan semua rating alternatif yang ada. Metode lain yang mampu digunakan dalam melaksanakan identifikasi kepada organisasi yang menjadi best in class dan mendapatkan solusi ideal adalah PROMETHEE. PROMETHEE (Preference Ranking Organization Method For Enrichment Evaluation) tergolong dalam keluarga sistem outranking yang dikembangkan oleh B. Roy (1985).
Metodologi Multicriteria outranking ialah pengembangan dari pendekatan tradisional dalam menentukan perusahaan yang memiliki kinerja terbaik. Metoda tersebut dapat menyingkir dari kelemahan dari metoda tradisional yang hanya berdasarkan pada agregasi kumpulan mono tolok ukur. PROMETHEE merupakan salah satu metode yang dipakai untuk memilih urutan atau prioritas dari beberapa alternatif dalam problem yang menggunakan multi standar.
PROMETHEE mempunyai kemampuan untuk mengatasi banyak perbandingan dan mempermudah pengguna dengan memakai data secara langsung dalam bentuk tabel multikriteria sederhana. Pengambil keputusan cuma mendefinisikan skala ukurannya sendiri tanpa batasan, untuk mengindikasi prioritasnya dan preferensi untuk setiap persyaratan dengan memusatkan pada nilai (value), tanpa memikirkan metoda perhitungannya.
2.3 Penentuan Prioritas Perbaikan
Langkah kedua dalam proses benchmarking adalah penentuan bagaimana tingkat-tingkat kinerja diraih. Oleh sebab itu, praktek terbaik perlu diidentifikasi sebagai masukan untuk perbaikan kinerja. Asrofah et al. (2010) menyimpulkan bahwa hasil kenali praktek terbaik berkontribusi pada efektivitas benchmarking di perusahaan manufaktur Indonesia. Reddy dan McCarthy (2006) memastikan bahwa praktek terbaik perlu dipromosikan setidak-tidaknya dengan memanfaatkan database yang mampu diakses oleh pihak yang memerlukan.
Faktor yang mesti diamati dalam mengidentifikasi praktek terbaik (Ungan, 2007) ialah kodifikasi, kompleksitas, dan kesesuaian. Praktek terbaik dapat didefinisikan dalam tiga level (Jaffar dan Zairi, 2000) yaitu
- Ide yang bagus (unproven);
- Praktek yang baik; dan
- Praktek terbaik (proven).
Ide yang baik – belum dibuktikan secara empiris dan perlu dilaksanakan analsis untuk menentukan ide tersebut akan memiliki dampak positif pada kinerja organisasi. Praktek yang bagus – berupa teknik, metodologi, mekanisme, atau proses yang sudah diimplementasikan dan telah meningkatkan kinerja organisasi. Praktek terbaik – praktek yang bagus yang sudah ditetapkan sebagai pendekatan terbaik bagi banyak organisasi berdasarkan hasil analisis data kinerja.
Maire et al. (2005) mengembangkan versi untuk mengidentifikasi praktek terbaik didasarkan pada prinsip yang sama dengan Quality Function Deployment (QFD). Namun, versi yang dirancang cuma dapat dipakai pada proses dan bukan pada produk jadi. Southard dan Parente (2007) berbagi metoda baru yang dipakai untuk proses evaluasi dalam perbaikan kinerja berdasarkan pada wawasan internal yang dimiliki. Pendekatan lain yang dapat dipakai untuk mengidentifikasi praktek terbaik ialah Root Cause Analysis (RCA).
RCA ialah pendekatan terstruktur untuk mengidentifikasi aspek-faktor besar lengan berkuasa pada satu atau lebih kejadiankejadian yang kemudian supaya dapat digunakan untuk memajukan kinerja (Corcoran, 2004). Selain itu, pemanfaatan RCA dalam analisis perbaikan kinerja berdasarkan Latino dan Kenneth (2006) dapat mempermudah pelacakan kepada aspek yang mempengaruhi kinerja. Root Cause(s) yaitu bab dari beberapa aspek (kejadian, keadaan, aspek organisasional) yang memberikan kontribusi, atau menjadikan kemungkinan penyebab dan diikuti oleh akhir yang tidak diperlukan.
Terdapat aneka macam metode evaluasi terstruktur untuk mengidentifikasi akar penyebab (root cause) sebuah kejadiaan yang tidak diharapkan (undesired outcome). Jing (2008) menjelaskan lima tata cara yang terkenal untuk mengidentifikasi akar penyebab (root cause) suatu kejadiaan yang tidak diharapkan (undesired outcome) dari yang sederhana hingga dengan komplek ialah :
- Is/Is not comparative analysis,
- 5 Why methods,
- Fishbone diagram,
- Cause and effect matrix, dan
- Root Cause Tree.
Is/Is not comparative analysis ialah metoda komparatif yang digunakan untuk problem sederhana, mampu memperlihatkan gambaran detil apa yang terjadi dan sudah sering dipakai untuk menginvestigasi akar persoalan. 5 Why methods merupakan alat analisis sederhana yang memungkinkan untuk menginvestigasi sebuah dilema secara mendalam. Fishbone diagram merupakan alat analisis yang populer, yang sangat baik untuk menginvestigasi penyebab dalam jumlah besar. Kelemahan terutama adalah kekerabatan antar penyebab tidak langsung terlihat, dan interaksi antar unsur tidak dapat teridentifikasi.
Cause and effect matrix ialah matriks alasannya akibat yang dituliskan dalam bentuk tabel dan memperlihatkan bobot pada setiap faktor penyebab dilema. Root Cause Tree ialah alat analisis sebab-akibat yang paling cocok untuk persoalan yang kompleks. Manfaat utama dari alat analisis tersebut ialah memungkinkan untuk mengidentifikasi hubungan diantara penyebab dilema. Chandler (2004) dalam Ramadhani et.al (2007) menyebutkan bahwa dalam mempergunakan RCA terdapat empat langkah yang mesti dijalankan ialah :
- Mengidentifikasi dan memperjelas definisi undesired outcome (suatu kejadiaan yang tidak dibutuhkan),
- Mengumpulkan data,
- Menempatkan peristiwa-peristiwa dan keadaan-keadaan pada event and causal factor table, dan
- Lanjutkan pertanyaan “mengapa” untuk mengidentifikasi root causes yang paling kritis.
Selanjutnya, langkah ketiga dari benchmarking yakni penggunaan gosip untuk pengembangan dan implementasi dari planning kenaikan. Oleh alasannya adalah itu, perlu dilakukan penentuan prioritas perbaikan. Hal ini dibutuhkan untuk mengenali perbaikan yang perlu mendapatkan prioritas, kemudian saran berdasarkan hasil analisis praktek terbaik diberikan.
Laugen et al. (2005) menyebutkan bahwa praktek terbaik yang menjadikan kinerja terbaik kadang kala susah untuk diidentifikasi. Davies (2000) menganjurkan pendekatan teratur (diagnostic) untuk menentukan praktek terbaik berdasarkan pada kekuatan hubungan dengan tujuan yang ingin dicapai.
3. METODOLOGI PENELITIAN
Untuk menghasilkan model konseptual analisis perbaikan kinerja industri gula dikerjakan tahapan selaku berikut :
- Melakukan kajian kepada banyak sekali buku referensi, jurnal-jurnal, laporan observasi terdahulu, pertimbangan para spesialis serta sumber lain yang dipandang akurat dan berhubungan .
- Identifikasi sub versi menurut tujuan tahap analisis perbaikan kinerja.
- Identifikasi keterkaitan antar sub versi.
- Identifikasi pendekatan yang dipakai untuk setiap sub model.
4. HASIL DAN PEMBAHASAN
Model konseptual analisis perbaikan kinerja pabrik gula (PG) yang dirancang bangkit terdiri dari 5 (lima) submodel yaitu:
- Sub model pengelompokan;
- Sub versi pengukuran kinerja;
- Sub model penyeleksian kinerja terbaik;
- Sub model analisis praktek terbaik; dan
- Sub model penentuan prioritas perbaikan.
Adapun secara ringkas versi konseptual ditunjukkan pada Gambar .
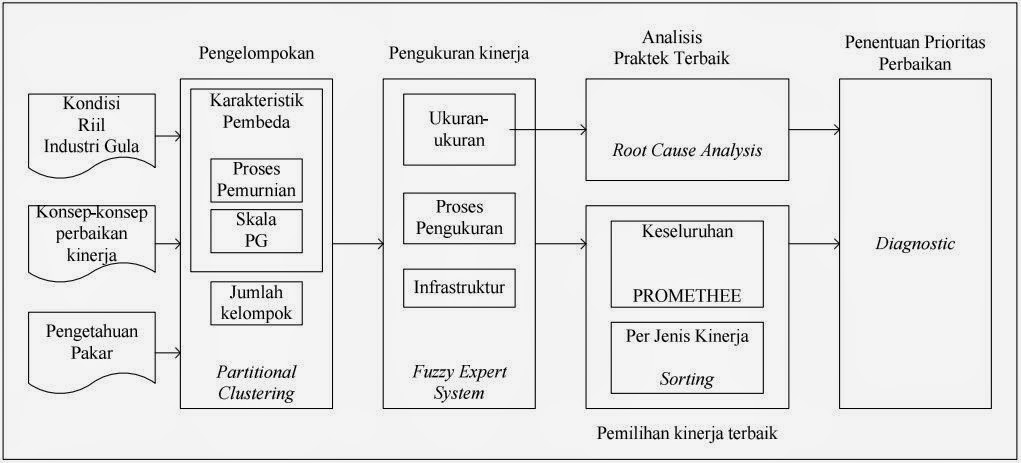
Gambar 1. Model Konseptual Analisis Perbaikan Kinerja Industri Gula
4.1 Model Pengelompokan
Model pengelompokan bermaksud untuk mengelompokkan pabrik gula yang mempunyai karakteristik yang sama. Pengelompokan pabrik gula (PG) diharapkan untuk menyetarakan pabrik gula sehingga layak untuk diperbandingkan. Untuk mengelompokkan PG yang mempunyai karakteristik serupa mampu dijalankan dengan mengelompokkan PG menurut karakteristik pembeda pabrik gula. Adapun karakteristik yang membedakan antar pabdik gula ialah tata cara yang dipakai dalam proses pemurnian dan skala pabrik gula.
Input model berbentukbasis data yang diharapkan untuk pengelompokan pabrik gula. Output dari versi pengelompokkan PG berbentukalternatif kelompok PG sesuai dengan karakteristik pembeda pabrik gula beserta anggota kelompoknya. Pendekatan yang digunakan untuk menggolongkan PG Merujuk pada Gan et al. (2007), Sadaaki et al. (2008), dan Xu dan Wunsch (2009) ialah supervised clustering (jumlah kelompok ditentukan) terutama Partitional clustering, cara untuk mengelompokkan data dalam satu cluster diadaptasi dengan skala evaluasi yang digunakan.
4.2 Model Pengukuran Kinerja
Kinerja yang akan diukur merujuk pada hasil penelitian Wibisono (1999, 2006), Radnor dan Barnes (2007), serta Cocca dan Albeti (2010) yakni kinerja strategis (kesanggupan sumber daya), kinerja operasional (tugas-tugas manufaktur), dan kinerja taktis (prioritas kompetisi). Ukuran kinerja yang hendak dipakai diidentifikasi dari range yang lebih luas ialah produktivitas dan efisiensi. Hal tersebut juga sesuai dengan masalah yang dihadapi oleh pabrik gula.
Sedangkan untuk keterkaitan ukuran kinerja, identifikasi ukuran kinerja akan dijalankan dengan penyelarasan secara vertikal (terkait dengan visi, misi, dan taktik industri gula) dan penyelarasan secara horisontal (keterkaitan antar ukuran kinerja dengan pendekatan input-proses-output). Dalam hal jumlah ukuran kinerja yang mau dipakai, model pengukuran kinerja memperhatikan aneka macam pendekatan pada observasi terdahulu (Medori dan Steeple, 2000; Denton, 2005; Shahin dan Mahbod, 2007; Saunders et al., 2007; Parmenter, 2010). Selain itu, penelitian Gleich et al. (2008) dan Martin (2008) pada proses manufaktur menjadi masukan dalam mengidentifikasi ukuran kinerja.
Kerangka kerja proses pengukuran kinerja mampu memanfaatkan akal fuzzy mirip yang dianjurkan dalam penelitian Chan et al. (2002) dan Beheshti dan Lollar (2008). Hal ini dijalankan mengingat adanya perbedaan satuan yang digunakan pada setiap ukuran kinerja. Adapun infrastruktur yang akan digunakan merujuk pada hasil penelitian Unahabhokha et al. (2007). Model pengukuran kinerja bermaksud untuk menentukan nilai kinerja setiap pabrik gula.
Pengukuran kinerja yang dikerjakan ialah untuk kinerja input, kinerja proses, dan kinerja output yang dinamakan kinerja strategis, kinerja operasional, dan kinerja taktis. Pengukuran kinerja dikerjakan kepada seluruh pabrik gula yang menjadi anggota untuk setiap alternatif kelompok pabrik gula. Oleh alasannya adalah itu, alternatif keputusan pada versi pengukuran kinerja pabrik gula yaitu seluruh pabrik gula yang menjadi objek kajian yang telah dikelompokkan berdasarkan karakteristik pembeda pabrik gula (ialah output dari versi pengelompokan pabrik gula).
Input model berupa basis data yang diperlukan untuk pengukuran kinerja. Output dari versi pengukuran kinerja berbentuknilai kinerja untuk setiap jenis kinerja pada seluruh anggota kelompok PG. Pendekatan yang digunakan dalam proses pengukuran kinerja pada model pengukuran kinerja yaitu Fuzzy Expert System (FES).
4.3 Model Pemilihan Kinerja Terbaik
Merujuk pada hasil observasi Dattakumar (2003), Grundberg (2003), Pierre dan Delisle (2006), Gleich et al. (2008) serta hasil penelitian Tucker (1987) yang membuktikan bahwa pendekatan benchmarking dapat meningkatkan efisiensi dan produktivitas perusahaan maka dalam penentuan target kinerja akan digunakan pendekatan benchmarking. Target kinerja diputuskan berdasarkan kinerja terbaik dalam kalangan (Tucker et. al. 1987).
Model Pemilihan Kinerja Terbaik bertujuan untuk menentukan pabrik gula berkinerja terbaik secara keseluruhan maupun untuk setiap jenis kinerja (kinerja strategis, kinerja operasional, kinerja taktis) pada setiap golongan pabrik gula. Hasil penyeleksian pada setiap golongan pabrik gula akan digunakan sebagai standar kinerja pembanding bagi setiap pabrik gula pada golongan yang serupa, baik untuk kinerja keseluruhan maupun per jenis kinerja. Nilai kinerja yang digunakan ialah nilai kinerja yang dihasilkan dari versi pengukuran kinerja yaitu nilai kinerja strategis, nilai kinerja operasional dan nilai kinerja taktis untuk seluruh pabrik gula yang menjadi anggota setiap alternatif golongan.
4.3.1 Pemilihan Kinerja
Terbaik secara keseluruhan Input model berbentukbasis data yang diperlukan untuk pemilihan kinerja terbaik secara keseluruhan. Output dari model berupa urutan (ranking/peringkat) pabrik gula dalam kelompok. Pemilihan kinerja terbaik secara keseluruhan dilaksanakan dengan menggunakan pendekatan PROMETHEE alasannya adalah memiliki kesesuaian dengan permasalahan yang dihadapi dan telah terbukti keunggulannya (mirip yang dikemukakan oleh Amran dan Kiki (2005), Prvlovic (2008), dan Triyanti dan Gadis (2008)).
4.3.2 Pemilihan Kinerja Terbaik Per Jenis Kinerja
Input versi berbentukbasis data yang dibutuhkan untuk pemilihan kinerja terbaik per jenis kinerja. Output dari model berbentukurutan (ranking) pabrik gula per jenis kinerja dalam kelompok. Pemilihan kinerja terbaik per jenis kinerja dilaksanakan dengan menggunakan pendekatan Sorting. Pendekatan Sorting memilih urutan kinerja terbaik per jenis kinerja dengan melakukan perbandingan antar nilai kinerja per jenis kinerja untuk seluruh PG pada setiap golongan PG. Nilai kinerja per jenis kinerja akan diurutkan dari yang nilainya terbesar hingga yang terkecil pada setiap kalangan.
4.4 Model Analisis Praktek
Terbaik Prioritas perbaikan diputuskan menurut praktek terbaik. Merujuk pada penelitian Jaffar dan Zairi (2000), maka analisis praktek terbaik ialah praktek yang baik yang telah ditetapkan sebagai pendekatan terbaik bagi banyak PG. Pendekatan yang digunakan dalam melakukan analisis praktek terbaik yang dianjurkan dalam observasi Maire et al (2005) dan Southard dan Parente (2007) mempunyai kelemahan mengenang praktek terbaik yang dihasilkan masih terbatas pada praktek yang baik (dilihat dari definisi praktek terbaik yang ditarik kesimpulan oleh Jaffar dan Zairi 2000).
Model Analisis Praktek Terbaik bertujuan untuk mengidentifikasi praktek terbaik yang menghasilkan kinerja terbaik. Input model berupa basis data yang diperlukan untuk analisis praktek terbaik. Output dari versi berupa keterkaitan antar ukuran kinerja yang digunakan dan faktor penyebab yang cukup penting untuk diperhitungkan serta identifikasi praktek terbaik yang mampu dilaksanakan pabrik gula. Merujuk pada penelitian Corcoran (2004) dan Latino dan Kenneth (2006) maka pendekatan yang digunakan untuk melakukan analisis praktek terbaik yaitu root cause analysis. Root cause analysis mampu dipakai untuk mengidentifikasi relasi alasannya akibat antar ukuran dan faktor (ukuran lain) yang menentukan kinerja.
4.5 Model Penentuan Prioritas Perbaikan
Penentuan prioritas perbaikan bertujuan untuk menentukan prioritas perbaikan yang mesti dikerjakan oleh PG. Input model berbentukbasis data yang diharapkan untuk penentuan prioritas perbaikan. Output dari versi berupa prioritas perbaikan yang mesti dilaksanakan oleh PG terkait dengan ukuran kinerja. Penentuan prioritas perbaikan menggunakan pendekatan yang menyerupai framework yang dikembangkan oleh Davies dan Kochar (2000) berbentukdiagnostik atau pencarian secara sistematis untuk menentukan praktek terbaik. Penelusuran secara sistematis dilakukan pada setiap kelompok pabrik gula. Untuk setiap pabrik gula yang akan diperbaiki maka kinerja keseluruhan, kinerja setiap jenis kinerja, dan kinerja setiap ukuran kinerja akan diperbandingkan dengan kinerja pabrik gula lain dalam kelompoknya.
5. KESIMPULAN
Analisis perbaikan kinerja mampu dilakukan dengan menggunakan versi analisis perbaikan kinerja yang berisikan 5 (lima) sub versi adalah pengelompokan, pengukuran kinerja, pemilihan kinerja terbaik, analisis praktek terbaik, dan penentuan prioritas perbaikan. Ke lima sub versi dirancangbangun saling terkait dimana output dari model pengelompokan akan menjadi bab dari input model pengukuran kinerja, output versi pengukuran kinerja akan menjadi bab dari input model penyeleksian kinerja terbaik dan input model analisis praktek terbaik, serta output dari versi penyeleksian kinerja terbaik dan model analisis praktek terbaik menjadi bab dari input model penentuan prioritas perbaikan. Oleh alasannya adalah itu, model analisis perbaikan kinerja yang dirancangbangun ialah versi yang terintegrasi untuk meraih tujuan dari analisis perbaikan kinerja yakni penentuan kinerja, penentuan target kinerja, dan penentuan prioritas perbaikan.
DAFTAR PUSTAKA
- [1] Amran TG, Kiki S. 2005. Pemilihan Partner Potensial Bahan baku kimia produk Fatigon Kaplet berdasarkan metode AHP dan Promethee di PT. Dankos Laboratories TBK. Di dalam : Prosiding Seminar Nasional Manajemen Kualitas ke-5. ISSN: 1907-0101-9-771907-010119. Jakarta.
- [2] Asrofah T, Zailani S, Fernando Y. 2010. Best Practices for the Effectiveness of Benchmarking in the Indonesian Manufacturing Companies. Benchmarking : An International Journal 17 (1) : 115 – 143. [3] Baxter LF, MacLeod AM. 2008. Managing Performance Improvement. New York : Routledge.
- [4] Beheshti HM, Lollar JG. 2008. Fuzzy Logic and Performance Evaluation : Discussion and Application. International Journal of Productivity and Performance Management 57 (3): 237 – 246.
- [5] Chan DCK, Yung, Andrew WH. 2002. An application of fuzzy sets to process performance evaluation. Integrated Manufacturing System 13(4): 237-246.
- [6] Cocca P., Alberti M. 2010. A Framework to Assess Performance Measurement Systems in SMEs. International Journal of Productivity and Performance Management 59 (2): 186-200. [7] Cokins G. 2004. Performance Management : Finding the Missing Pieces (to Close the Intelligence Gap). New Jersey : John Wiley & Sons.
- [8] Daellenbach HG, McNickle DC. 2005. Management Science : Decision Making Through System Thinking. New York : Palgrave Macmillan.
- [9] Dattakumar R, Jagadeesh R. 2003. A Review of literature on Benchmarking. Benchmarking: An International Journal 10 (3): 176-209.
- [10] Davies AJ, Kochhar AK. 2000. A Framework for the Selection of Best Practices. International Journal of Operations & Production Management 20 (10): 1203-1217.
- [11] Denton DK. 2010. Performance Measurement and Intranets : A Natural Partnership. International Journal of Productivity and Performance Management 59 (7): 701-706.
- [12] Denton DK. 2005. Measuring Relevant Things. International Journal of Productivity and Performance Management 54 (4):278 – 287.
- [13] Dragolea L, Cotirlea D. 2009. Benchmarking-A Valid Strategy for the Long Term?. Annales Universitatis Apulensis Series Oeconomica 11 (2) : 813 – 826.
- [14] Effendi A. 2009. Teknologi Gula. Jakarta : Penerbit BeeMarketer Institute.
- [15] Elmuti D, Yunus K. 1997. An Overview of Benchmarking Process : A Tool for Continuous Improvement and Competitive Advantage. Benchmarking for Quality Management & Technology 4 ( 4): 229-243.
- [16] Gan G, Chaoqun M, Wu J. 2007. Data Clustering. United States of America : The America Statistic Association. [17] Gleich R, Motwani J, dan Wald A. 2008. Process Benchmarking : A New Tool to Improve The Performance of Overhead Areas. Benchmarking : An International Journal 15 (3): 242-256.
- [18] Grundberg T. 2003. A Review of Improvement Methods in Manufacturing Operations. International Journal of Productivity and Performance Management 52 (2) : 89-93.
- [19] Halachmi A. 2005. Performance Measurement is Only One Way of Managing Performance. International Journal of Productivity and Performance Management 54 (7): 502- 516.
- [20] Jafari M, Bourouni A, Amiri RH. 2009. A New Framework for Selection of the Best Performance Appraisal Method. European Journal of Social Sciences 7 (3): 92-100. [21] Jaffar YF, Zairi M. 2000. Internal Transfer of Best Practice for Performance Excellence : A Global Survey. Benchmarking : An International Journal 7 (4): 239-246.
- [22] Jing GG. 2008. Diging for the Root Cause. ASQ Six Sigma Forum Magazine 7 (3): 19-24.
- [23] Kusumadewi S, Hartati S, Harjoko S, Wardoyo R. 2006. Fuzzy Multiattribute Decision Making. Yogyakarta: Penerbit Graha Ilmu.
- [24] Laise D. 2004. Benchmarking and learning organizations : ranking methods to identify “best in class”. Benchmarking : An International Journal 11 (6): 621-630.
- [25] Latino RJ, Kenneth CL. 2006. Root Cause Analysis : Improving Performance for Bottom – Line Results. Florida : CRC Press. [26] Laugen BT, Acur N, Boer H. 2005. Best Manufacturing Practices : What do the Best-Performing Companies Do?. International Journal of Operations & Production Management 25 (2): 131-150.
- [27] [LPPM-IPB] Lembaga Penelitian IPB. 2002. Studi Pengembangan Agribisnis Pergulaan Nasional. [28] [LPPM-IPB] Lembaga Penelitian IPB. 2002. Studi Pengembangan Sistem Industri Pergulaan Nasional.
- [29] Maire JL, Vincent B, Maurice P. 2005 A Typology of “Best Practices” for a Benchmarking Process. Benchmarking : An International Journal 12 (1): 45-60.
- [30] Manalu LP. 2009. Analisis Kinerja Pabrik Gula Dengan Metoda DEA (Data Envelopment Analysis). Jurnal
ABSTRACT
Research related to the analysis of performance improvement (as used in a systematic process to identify performance, determine the desired performance targets, and to determine the priority of improvement at the sugar industry in Indonesia has not been done. This research aims to produce a conceptual model that can be used to analyze the sugar industry performance improvement. The versi produced an integrated model to achieve the objectives of the analysis phase of performance improvement. The resulting versi consists of five sub-models : 1) grouping, 2) performance measurement, 3) selection of the best performance, 4) analysis of best practices, and 5) determination of priorities for improvement.
Keywords : conceptual versi, analysis of performance improvement, sugar industry